15+ человек, которые на собственном опыте убедились, что закончить ремонт ой как непросто
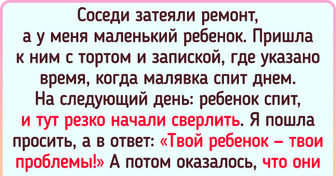
Кола, Фанта, Спрайт, энергетический напиток... Почти все алюминиевые банки имеют цилиндрическую форму. Вы никогда не задумывались, почему? Представьте, что вы производитель напитка и вам нужно придумать самую эффективную форму банки. Нужно, чтобы она была максимально удобной для клиента, а еще вы хотите свести затраты материалов к минимуму и оптимально использовать пространство. Лучше всего — банка в виде сферы. Для такой банки понадобится минимальное количество материала. Кроме того, у нее не будет углов, и давление будет одинаковым в каждой ее точке. В ней не будет слабых мест, и банка выдержит огромное давление.
Звучит здорово, но есть пара проблем. Прежде всего сфера не может стоять на месте. Она будет скатываться со стола, а это непрактично. Даже если делать дно плоским, есть еще одна проблема — упаковка для перевозки. Если упаковать банки максимально эффективно, всё равно будет использовано лишь семьдесят четыре процента пространства коробки и останется много пустоты. Больше четверти. То же относится и к полкам магазинов: придется выставлять меньше товаров этой формы. Выходит, сфера неэффективна, когда дело доходит до хранения жидкостей.
Еще какие-нибудь идеи? Самая эффективная форма для хранения и выставления — это кубоид. Такие банки будут занимать сто процентов места при упаковке или на полках. Дно будет плоским, и они будут очень устойчивыми. Однако у такой формы много слабых мест: это ребра. Они могут сломаться из-за внутреннего давления или при падении банки. Инженеры придумали нечто среднее между этими двумя вариантами — цилиндрическую форму. Она близка к кубической в плане эффективности упаковки: она занимает до девяноста одного процента места. И у нее нет слабых мест, как у сферической банки, потому что нет ребер. Итак, выбор был очевиден, и большинство производителей это поняли.
Хотите знать, как делается банка? Итак, это обычный алюминиевый диск. Он выглядит намного толще банки потому, что это весь материал, который нужен для ее изготовления. Диск помещают между двумя дисками в форме пончиков с отверстием посередине. Затем цилиндрический пуансон давит на него сверху, превращая в маленькую чашечку. Эта чашка всё еще немного шире, чем банка, и при этом намного ниже. Итак, нужна еще пара шагов. Эта чашка идет под пресс меньшего диаметра, и пуансон еще раз нажимает на чашку.
Теперь чашка стала меньше в диаметре и немного выше. Еще немного усилий, и получается нужный диаметр! Но она всё еще слишком низкая. Следующий шаг — сделать стенки немного тоньше. Алюминий со стенок как раз увеличит высоту чашки. Итак, еще один удар проталкивает чашку через гладильное кольцо, и ее стенки становятся заметно тоньше и выше. Далее на дне чашки нужно сделать купол. Пуансон толкает чашку на выступающий механизм. Сам пуансон имеет соответствующее вогнутое углубление, и при нажатии дно чашки деформируется в купол.
Купол нужен для большей эффективности. Вогнутое дно требует меньше материала, чем плоское. И оно более устойчиво к давлению. Кривая помогает превратить часть вертикального давления в горизонтальное, поэтому купол выдерживает большее давление, чем плоскость. Чтобы убедиться, что давление сохраняется, попробуйте сжать пустую банку. Это просто. А теперь попробуйте сжать полную банку. Уже сложнее. А всё потому, что есть внутреннее давление. Оно сопротивляется сжатию и сильно его затрудняет. Вернемся к банке. После всех деформаций края банки становятся неровными. Что ж, давайте их срежем, чтобы было красиво и ровно. Пора напечатать внешний дизайн, и банка будет почти готова.
Большинство банок сверху сужаются. Поэтому нужно вставить внутреннюю матрицу меньшего диаметра, чем у банки, в корпус банки, а затем плотно прижать к ней внешнюю матрицу. Это можно повторить несколько раз, чтобы убедиться, что банка будет ровной. Осталось добавить верхнюю крышку, и банка готова! Идем дальше. Есть какие-нибудь догадки, что это такое? Это пластиковая бутылка будущего! Она сделана из пластиковых хлопьев, называемых ПЭТ. Обычно их смешивают со стружкой переработанного пластика. Нельзя сделать бутылку из одного лишь переработанного пластика, потому что она потеряет важные свойства.
Эта смесь поступает в инжекционную машину, которая нагревает ее и плавит стружку в густую жидкость. Затем другая машина выталкивает жидкость в шаблон цилиндрической формы с системой охлаждения, и всё затвердевает. Получаются твердые прозрачные пластиковые трубки. Они попадают в другую машину, которая нагревает их ровно настолько, чтобы растянуть. Туда вставляют заготовку в форме будущей бутылки. Затем под высоким давлением подается воздух, чтобы растянуть заготовку до нужной формы. После этого пластик охлаждается, чтобы зафиксировалась форма.
У пластиковых бутылок почти плоское дно, кроме небольшого изгиба. И это неслучайно. Дело в том, что на дне бутылки всегда будет иметься изгиб, который сделает ее неустойчивой. Чтобы этого избежать, вниз подается немного воздуха, и у основания получается небольшой пунт. А вот и бутылка. Банки с арахисовым маслом и медом делают так же. Они могут быть разных видов, и из этих заготовок можно сделать любую форму. У бутылок из пластика для безалкогольных напитков на дне есть пять выступов. Плоские донышки удобны, потому что для их изготовления требуется меньше пластика. Но безалкогольные напитки и газированная вода нуждаются в особом обращении. У этих жидкостей есть внутреннее давление, которое выталкивает пластик наружу, разрушая пунт и устойчивую форму бутылки.
Бутылки с газировкой делают изогнутыми, потому что так они становятся более устойчивыми к давлению. Сравните складывание обычного листа бумаги со складыванием трубки. Трубка будет иметь большее сопротивление. Изогнутый пластик тоже более устойчив к давлению. Стекло изготавливается из нескольких видов натурального сырья. Основные компоненты — это кварцевый песок, который составляет сорок пять процентов всей смеси. Кальцинированная сода — пятнадцать процентов смеси. За счет нее песок плавится равномерно. Известняк составляет около десяти процентов и делает стекло более прочным. Чтобы изготовить стеклянную бутылку, сначала смешивается всё необходимое сырье, а затем смесь нагревается до полутора тысяч градусов Цельсия. Когда всё это плавится, получается липкая слизь, которая выливается из машины и разрезается на ровные куски.
Затем каждый кусок расплавленного стекла попадает в первую форму, которая превращает его в заготовку-полуфабрикат. Каждая заготовка помещается в стальную форму, которая определяет итоговый облик. Так что, если вы хотите сделать бутылку с особыми элементами дизайна, это именно тот этап, на котором нужно добавить их в форму. Заготовка снова нагревается, и оборудование направляет сжатый воздух внутрь, растягивая стекло до конечной формы. Теперь бутылка почти готова. На выходе она проходит через огонь. Если она остынет слишком быстро, то треснет от теплового удара. Упс, падение температуры было слишком быстрым! Это всё равно, что налить ледяную воду в горячий стакан. Машины охлаждают бутылки медленно, шаг за шагом. После этого стеклянная бутылка готова к употреблению.
Стеклянные бутылки могут быть разных цветов, но чаще всего они белые, зеленые и коричневые. Разные цвета получаются путем добавления разных компонентов в первичную смесь до нагревания. Если смесь будет без добавок, бутылки или банки получатся просто прозрачными. Чтобы стекло стало коричневым, в смесь нужно добавить железо, серу и углерод. Для зеленой бутылки нужно добавить железо, хром и медь. А если добавить оксид кобальта и медь, то бутылка станет синей. Вот такая яркая история!